Table of contents
Table of contents
Abrasive deslurry for waterjet cutting systems
A sustainable and cost-saving investment
Whoever says ‘abrasive waterjet cutting‘ should also say ‘abrasive desludging’.
When cutting with abrasive sand at high performance, a not to be underestimated amount of waste material is produced whose disposal can quickly become a challenge.
Particularly in a multi-shift cutting operation, the need for clever and efficient solutions for separating water and abrasive arises here.
As part of the STM modular system, we offer an additional module system for abrasive flushing in the abrasive cutting process.
The STM BasicClean and STM OneClean abrasive rinsing systems take over fully automated cleaning of the water-abrasive mixture during and after the cutting process.
The advantages cannot be denied:
With the STM OneClean modules, water and abrasive can not only be separated, but also cleaned to a large extent and reused for the cutting process. This sustainably reduces operating costs and also promotes environmental awareness, which is playing an increasingly important role in the industry.
The STM OneClean as well as OneClean+ are systems for abrasive application based on the modular principle. This is because the abrasive rinsing modules can be individually combined and supplemented here.
The STM BasicClean and STM BasicClean+, a suitable entry-level model, provide the entry-level in the field of abrasive desludging. This abrasive removal system is the economical entry into efficient abrasive removal for waterjet cutting systems and offers a fully automatic, space-saving abrasive removal system for collecting the settled abrasive sand.
OneClean & OneClean+
Modular system for reprocessing and cleaning
Reduce operational costs and increase profits. STM OneClean/OneClean+, the modular all-round systems for recycling and cleaning abrasive and water, enables you to operate your waterjet cutting system even more sustainably.
The STM basic idea of organically and modularly adapting waterjet cutting systems to the customer’s requirements in order to cut even more economically and efficiently is evident in all aspects of the OneClean system. The plant can be put into operation with a small investment and expanded at any time as needed.
Four interrelated modules allow you to customize the system specifically to your own requirements. All modules of the OneClean system consist without exception of high-quality brand components co-developed by STM. Solid aluminum construction throughout ensures maximum wear resistance and load capacity.
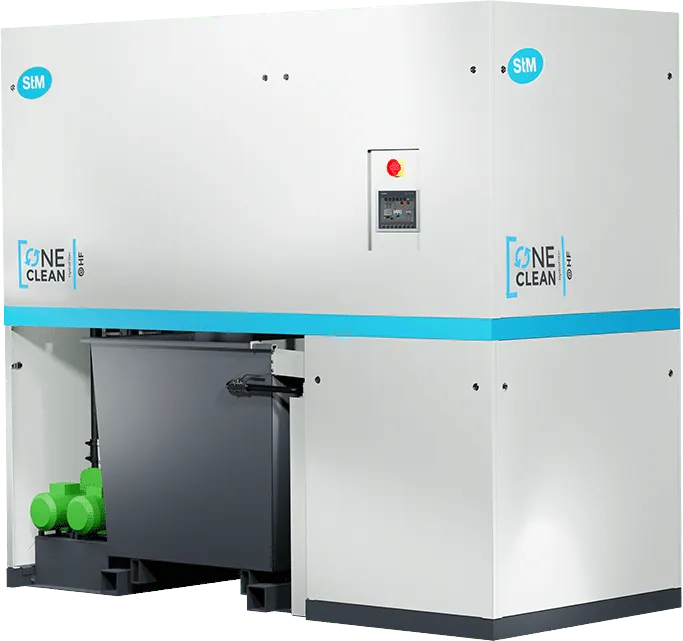
OneClean modules
The modules of the OneClean abrasive rinsing system can be individually combined and supplemented – according to your requirements. Thanks to the modern process visualization with touch display, the operator is informed about all processes at a glance.
Module 1 – Hydrofilter
The OneClean hydrofilter is the heart of the STM OneClean modular system. The module uses a highly wear-resistant coated electric pump to convey the water-abrasive mixture from the cutting basin and separates the used abrasive from the process water.
The hydrofilter switches on automatically when cutting with abrasive and switches off again after the cutting process at the end of a short follow-up time. It separates abrasive from the process water into a BigBag. The collection container with the BigBag can be pulled out of the holding device by means of a lift truck.
Module 2 – Pressure bag filter
The pressure bag filter additionally cleans the wastewater before it is discharged into the sewer.
For the cutting itself, approx. 100 – 300 liters of water per hour are fed to the pressure bag filter, depending on the high-pressure pump capacity. The pressure bag filter can be integrated into the OneClean system or used as a “standalone” solution.
Module 3 – Water treatment
Before installing an STM system, the water values are analyzed and compared to the specially developed stability index. High pressure pump manufacturers recommend appropriate treatment of the water in case of deviations.
In water treatment, a dosing pump adds a water additive in minute, precisely dosed quantities to the supply water of the high-pressure pump, bringing it into balance. The advantages are longer service lives for high-pressure seals and water nozzles.
Module 4 – Water circulation system
The water circulation system cleans the process water so thoroughly that it can be fed back into the high-pressure pump without hesitation. The separation limit of less than 1 µm is achieved with the ultrafiltration used.
Upstream is a cascade of settling clarifiers and filters that are automatically flushed and monitored by PLC. A water treatment completes the cleaning step. When using the water circulation system, only the water that is lost through evaporation needs to be replaced.
Advantages OneClean & OneClean+
Specifications OneClean & OneClean+
- 1-stage settling tank with high-performance pumps, efficient double cyclones for rapid separation of the process water from the abrasive sand
- Removable collection container with weighing system
- Level basin for regulating the water level in the cutting basin
- Control for automatic switching on and off linked to the cutting process
- Special ceramic-coated, long-life, high-performance pumps
- Piping and PLC with display
- Submersible pressure pump as pumping/lifting station for discharging the water into the canal
- Uniform size across all variants
- Length x width x height: 2,600 x 1,200 x 2,270 mm
- Unladen weight: approx. 450 kg
- Pressure bag filter for additional filtration before sewer discharge
- Upstream coarse particle filter: filters coarse particles from the cutting basin as a preliminary stage to protect the high-performance pumps
- “OneClean+” variant with an additional double cyclone and two additional pumps
- Flocculator
BasicClean & BasicClean+
Automatic, space-saving abrasive rinsing system with BigBag
The STM BasicClean and STM BasicClean+ abrasive dispensing systems provide you with an economical introduction to efficient abrasive rinsing for waterjet cutting systems.
The used abrasive is flushed out of the cutting basin with the automatic abrasive flushing system. A ceramic-coated high-performance pump sucks the water-abrasive mixture out of the cutting basin via the suction filter. The abrasive then settles in a BigBag, which weighs approx. 2 t when filled. The second high-performance pump in turn conveys the process water separated from the abrasive back into the cutting basin. The control takes place automatically via a PLC. The automatic abrasive rinsing system switches on automatically when cutting with abrasive sand and switches off again after the cutting process with a follow-up time. When the BigBag is full, they are lifted out of the settling tank to dry and replaced by an empty BigBag.
Specifications BasicClean & BasicClean+
- 1-stage settling tank with high-performance pumps, efficient cyclone for rapid separation of the process water from the abrasive sand
- Stilling basin (available in three sizes, 250, 500 or 750 liters, depending on the size of the waterjet cutting system and the level control of the cutting basin)
- Control for automatic switching on and off linked to the cutting process
- Special ceramic-coated, long-life, high-performance pumps
- Piping and PLC
- Length (depending on level basin): 2,405 mm (250 liters) / 2,960 mm (500 liters) / 3,525 mm (750 liters)
- Width x height: 1.202 x 1.750 mm
- Empty weight: approx. 300 kg
- Upstream coarse particle filter: filters coarse particles from the cutting basin as a preliminary stage to protect the high-performance pumps
- “BasicClean+” variant with additional hydrocyclone and two additional pumps for double rinsing capacity
- Pressure bag filter as pumping/lifting station for additional filtration before sewer discharge
- Submersible pressure pump as pumping/lifting station for discharging the water into the canal
Advantages BasicClean & BasicClean+
Material diversity
Waterjet cutting offers unlimited possibilities
With the waterjet technology can almost any material, whether metal, stone, glass, plastic and more. to be edited. It is a cold cutting process with high precision and quality.
We explain how it works, what types & techniques are available and in which industries it is used.